Applicare alla propria azienda un modello industriale sostenibile significa adottare processi produttivi e gestionali che riducono l’impatto ambientale, ottimizzano l’uso delle risorse e promuovono il benessere sociale ed economico nel lungo termine. Anticipando da sempre il futuro, nel 2000 RIMSA ha avviato un processo di digitalizzazione aziendale che di concretizza oggi in un sistema di gestione integrato che connette uomo e macchina in maniera sostenibile e responsabile.
Modello RIMSA
Industria Sostenibile
Digitalizzazione: da strumento applicativo a cultura aziendale
Come l’Industria 4.0 ridefinisce processi, tecnologie e metodologie in un contesto produttivo integrato
Nel contesto della trasformazione tecnologica e dell’evoluzione dei modelli produttivi, RIMSA ha avviato nel 2000 un percorso verso la digitalizzazione 4.0 anticipando i tempi. La graduale introduzione di strumenti operativi d’avanguardia si è progressivamente integrata nei valori e nei processi aziendali fino a diventare una vera e propria cultura d’impresa, sostenibile, responsabile e orientata al futuro.
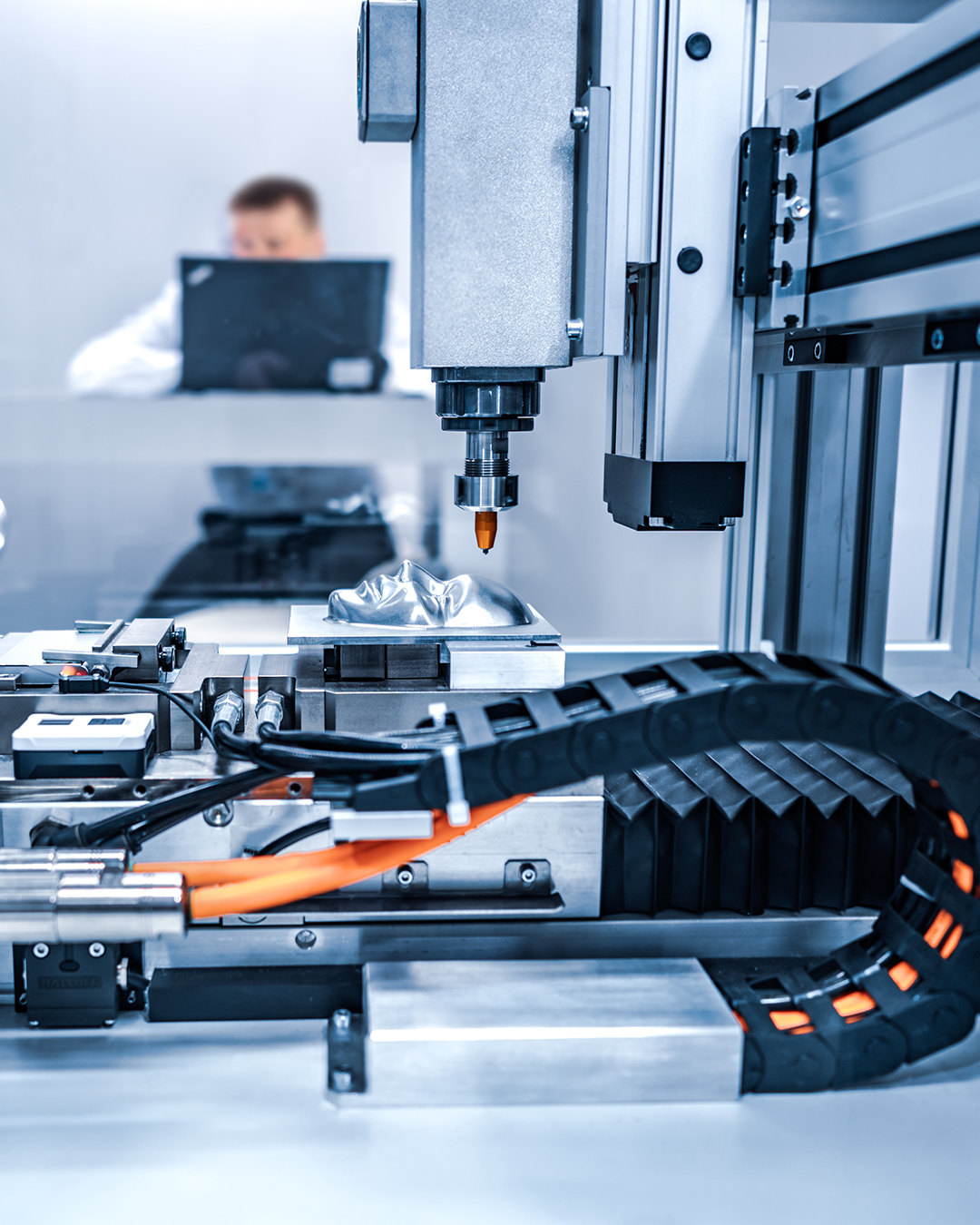
1
Introduzione all’industria 4.0
Con l’avvento dell’Industria 4.0, le aziende stanno vivendo una profonda trasformazione che investe infrastrutture, sistemi di gestione e cultura organizzativa.
Se in passato la spinta verso l’automazione si concentrava prevalentemente sulla meccanizzazione e sul controllo di processo, oggi l’innovazione riguarda soprattutto l’integrazione digitale dei vari reparti e la capacità di connettere macchinari, software e persone in un unico ecosistema. L’Industria 4.0 porta con sé diversi concetti chiave. Tra i principali troviamo la digitalizzazione dei flussi informativi, l’interconnessione tra dispositivi e sistemi, l’integrazione del software a tutti i livelli, l’analisi dei dati in tempo reale, la manutenzione e analisi predittiva, nonché la verticalizzazione dei processi interni che punta ad accorciare la catena del valore. In quest’ottica, RIMSA rappresenta un esempio virtuoso di come una PMI (Piccola e Media Impresa) possa intraprendere un percorso di digitalizzazione capillare e coerente, trasformando il proprio modello operativo.
2
Fondamenti dell’industria 4.0
I fondamenti dell’Industria 4.0 si basano su concetti chiave che definiscono l’evoluzione dei processi produttivi verso un modello sempre più connesso, automatizzato e intelligente.
Prima di avventurarci nell’approfondimento di come RIMSA sia esempio di azienda 4.0 si offrono delle definizioni.
Digitalizzazione
Digitalizzare significa convertire i processi da analogici a digitali, ma non si tratta di una semplice sostituzione di documenti cartacei con file informatici. È, piuttosto, l’opportunità di ridisegnare intere procedure, sfruttando dati in tempo reale e software sempre più sofisticati per agevolare la comunicazione tra reparti. In RIMSA, ciò si traduce in una gestione integrata dei flussi di progetto, della produzione e della logistica, con sistemi che “parlano” tra loro e condividono informazioni in modo automatico.
Interconnessione
La vera forza dell’Industria 4.0 risiede nella capacità di collegare macchine, sensori, software e persone in un network intelligente. Ogni componente fornisce e riceve dati, e tali informazioni vengono elaborate per prendere decisioni più rapide ed efficienti. Nella pratica, questo significa che un macchinario di verniciatura, ad esempio, può comunicare in tempo reale con il sistema gestionale (ERP o MRP), segnalando eventuali scostamenti di produzione o necessità di manutenzione. Allo stesso modo, i reparti di progettazione, qualità e produzione restano costantemente sincronizzati.
Integrazione (anche di software)
Parlare di integrazione software vuol dire creare un “ecosistema digitale” dove CRM, ERP, MRP, PLM, sistemi CAM e strumenti di business intelligence interagiscano in modo sinergico. Questo approccio permette di ridurre i cosiddetti “silos” aziendali, che spesso rallentano la condivisione di informazioni tra uffici diversi. In RIMSA, ad esempio, il disegno 3D di un componente può essere caricato su un sistema PLM, reso accessibile all’ufficio qualità e, contestualmente, dialogare con l’MRP per aggiornare i cicli di lavorazione e le distinte base.
Analisi dati
I dati sono il “carburante” dell’Industria 4.0. La capacità di raccoglierli, elaborarli e interpretarli in tempo reale consente di prendere decisioni strategiche basate su evidenze oggettive, anziché su semplici ipotesi. Dalle informazioni di produzione alle metriche di vendita, passando per l’andamento del magazzino e la tracciabilità dei componenti, tutto confluisce in un archivio digitale che permette di costruire KPI (Key Performance Indicator) chiari e di monitorare costantemente l’efficienza operativa.
Analisi predittiva
Un passo ulteriore rispetto alla tradizionale Business Intelligence è la manutenzione predittiva e, in generale, l’analisi che anticipa eventi futuri. Utilizzando algoritmi di machine learning o statistici, l’azienda può prevedere quando un macchinario avrà bisogno di manutenzione, evitando fermi produzione improvvisi. Analogamente, i dati di vendita possono essere sfruttati per prevedere i picchi di domanda e ottimizzare le scorte di magazzino. RIMSA, in questo modo, riduce i tempi morti e ottimizza i processi, distribuendo le risorse in modo più puntuale.
Verticalizzazione
La verticalizzazione dei processi, o l’accorciamento della catena del valore, significa internalizzare determinate fasi produttive o di progettazione, riducendo la dipendenza da fornitori esterni e aumentando il controllo diretto su qualità e tempi di consegna. In un’ottica Industria 4.0, la verticalizzazione non è solo “avere tutto in casa”, ma piuttosto gestire con trasparenza e tracciabilità ogni passaggio, collegando sistemi e processi per garantire coerenza e rapidità di esecuzione. In RIMSA, ciò si traduce nell’internalizzazione di alcune lavorazioni e nella stretta integrazione digitale con i fornitori selezionati, ai quali viene chiesta la medesima affidabilità e competenza, inclusa la condivisione di report e test di qualità.
3
Controllo e tracciabilità: i vantaggi dell’industria 4.0 per le aziende
Un ambiente completamente digitalizzato e integrato consente di sapere in ogni momento dove si trovano i materiali, a che punto è una lavorazione e quali test sono stati effettuati su un determinato componente. In questo modo, l’azienda non solo riduce errori e rilavorazioni, ma può intervenire prontamente in caso di anomalie.
Riduzione dei costi e degli sprechi
Digitalizzare significa rendere i processi più snelli, eliminando passaggi superflui e riducendo la duplicazione di dati o documenti. Inoltre, una migliore pianificazione consente di ottimizzare l’uso delle risorse (materie prime, tempo, personale). Nel caso di RIMSA, il controllo puntuale dei cicli di produzione e la gestione sincronizzata del magazzino attraverso l’MRP abbattono gli sprechi sia in termini di scorte eccessive, sia di produzioni non più richieste dal mercato.
Il Passaporto Digitale
Da RIMSA, ogni pezzo prodotto ottiene un passaporto digitale, in cui si raccolgono i dati di lavorazione, i seriali dei componenti, i test eseguiti e i risultati. Se un componente risulta non conforme, si risale immediatamente alla sua origine, migliorando il time-to-resolution.
Riduzione dei costi e degli sprechi
Digitalizzare significa rendere i processi più snelli, eliminando passaggi superflui e riducendo la duplicazione di dati o documenti. Inoltre, una migliore pianificazione consente di ottimizzare l’uso delle risorse (materie prime, tempo, personale). Nel caso di RIMSA, il controllo puntuale dei cicli di produzione e la gestione sincronizzata del magazzino attraverso l’MRP abbattono gli sprechi sia in termini di scorte eccessive, sia di produzioni non più richieste dal mercato.
Efficientamento energetico
Con l’Industria 4.0, la sostenibilità non è più un semplice obiettivo a lungo termine, ma diventa parte integrante del sistema produttivo. L’analisi in tempo reale dei consumi e l’adozione di tecnologie “smart” (LED, macchine di ultima generazione) permettono di gestire l’energia in modo più razionale. Per esempio, se il sistema rileva un calo nella domanda produttiva, spegne o rallenta automaticamente determinate linee, riducendo gli sprechi energetici. A ciò si aggiunge la possibilità di monitorare le emissioni di CO₂ e implementare strategie di compensazione ambientale.
Sostenibilità sociale
Un ambiente digitalizzato non è solo più efficiente, ma anche più stimolante per i lavoratori. Avere strumenti software intuitivi (tablet, interfacce grafiche semplificate) e processi trasparenti aumenta il senso di appartenenza, facilitando la collaborazione e la formazione continua. La possibilità di acquisire nuove competenze — anche in autonomia, grazie ai Learning Management System (LMS)— crea opportunità di crescita personale. RIMSA, infatti, incentiva l’aggiornamento professionale, permettendo ai propri dipendenti di formarsi su diversi macchinari e processi, facilitando possibili mobilità interne.
Miglioramento qualità
Qualità significa conformità alle specifiche e soddisfazione del cliente. In un sistema connesso, i controlli di qualità possono avvenire in ogni fase, dall’accettazione materie prime al collaudo finale, con report che si “agganciano” in automatico al seriale del prodotto o del componente. L’integrazione tra disegno 3D, PLM e software di misura evita errori di trascrizione o versioni datate, perché ogni revisione viene recepita in tempo reale e i macchinari non avviano la produzione finché non c’è piena corrispondenza tra disegno e cicli di lavorazione.
4
Digitalizzazione in azienda: l’esempio di RIMSA
RIMSA ha intrapreso un percorso di digitalizzazione che abbraccia tutti i reparti. La trasformazione non è avvenuta in un giorno, ma passo dopo passo, grazie a una visione chiara e a investimenti continui in software, macchinari e formazione del personale.
Dall’ufficio tecnico alla produzione
In RIMSA, il disegnatore realizza un modello 3D utilizzando un software CAD avanzato. Questo file viene subito caricato nel PLM, dove è accessibile al reparto qualità, all’ufficio acquisti e alla produzione. Grazie a una personalizzazione del software, il responsabile qualità inserisce direttamente le tolleranze da verificare nelle varie fasi (accettazione, pre-lavorazione, post-lavorazione). L’MRP, integrato con il PLM, aggiorna in automatico i dati relativi ai piani di controllo e agli strumenti di misura, evitando trascrizioni manuali e riducendo gli errori.
Parallelamente, il responsabile di produzione definisce il ciclo produttivo attraverso un’interfaccia grafica semplificata, associando a ogni fase i componenti da utilizzare e le eventuali macchine coinvolte. Il responsabile tempi e metodi, invece, specifica i tempi standard di realizzazione di ogni singolo componente, incrociando i dati con i consuntivi provenienti dal reparto produttivo. Questo flusso continuo di informazioni garantisce un costante adeguamento dei cicli di lavoro alla realtà effettiva, migliorando la precisione e la tempestività di ogni decisione.
Interazione uomo-macchina e controllo CAM
Uno dei pilastri dell’Industria 4.0 è l’interazione diretta tra persone, macchinari e sistemi. In RIMSA, i macchinari utensili attingono i programmi di lavorazione direttamente dal PLM aziendale. Se un disegnatore aggiorna il progetto, la macchina confronta la versione del disegno con la revisione del programma CAM; se trova una discrepanza, blocca la produzione finché il responsabile CAM non rilascia la versione corretta. Questo riduce drasticamente gli errori di lavorazione causati da incongruenze tra disegno e programmi macchina.
Logistica interna, distinta base e magazzino
La digitalizzazione interessa anche la logistica interna: la distinta base per ogni articolo comprende non solo i componenti necessari, ma anche le fasi di lavorazione e il relativo fabbisogno. Appena una fase è lanciata, il sistema gestionale invia un ordine di prelievo al magazzino, indicando le quantità esatte da movimentare e il momento in cui servono. Ciò migliora l’organizzazione del magazzino e la chiarezza per gli operatori, che possono preparare il carrello di lavoro in modo sequenziale, evitandosi giri a vuoto o ricerche inutili.
Postazioni di lavoro “smart” e formazione continua
Ogni operatore in linea di produzione dispone di un tablet, tramite cui accedere ai dati necessari (disegni 3D in modalità visualizzatore, schede di montaggio, materiali disponibili). In caso di dubbi, può consultare in tempo reale l’LMS aziendale, guardare tutorial sulle fasi di assemblaggio e, se interessato, formarsi su altre lavorazioni. Questa “apertura” formativa permette di aumentare il livello di competenza degli operatori e di facilitare il trasferimento interno di ruoli e mansioni, agevolando la mobilità orizzontale e verticale delle risorse umane.
Tracciabilità totale e passaporto digitale del prodotto
In RIMSA, ogni macchina di collaudo e test genera un report digitale collegato al lotto o al seriale del componente. Ogni trasformazione significativa si traduce in un numero di serie univoco, che confluisce poi in quello del prodotto finale. Se un cliente fornisce la matricola del prodotto, l’azienda può risalire in pochi secondi a tutti i test e ai risultati, nonché ai seriali dei componenti interni. È una tracciabilità a 360°, preziosa anche per la manutenzione post-vendita, perché garantisce che un eventuale ricambio corrisponda esattamente ai parametri originali, assicurando continuità di prestazioni.
KPI e JIT
Una volta che i dati fluiscono in modo uniforme tra i reparti, diventa semplice tenere sotto controllo KPI come la produttività, i tempi di fermo macchina, la resa di ogni operatore e le non conformità. Il Just In Time (JIT), che prevede la produzione solo quando effettivamente necessaria, viene supportato da una pianificazione in tempo reale, riducendo le scorte di magazzino e garantendo tempi di consegna più rapidi.
Collaborazione con i fornitori
La qualità non si limita all’interno dell’azienda: RIMSA richiede ai fornitori la stessa trasparenza, fornendo linee guida e protocolli di test. Per ogni componente esterno, il fornitore genera report completi, assicurando che la catena di fornitura sia affidabile e tracciabile. Anche questi dati confluiscono negli archivi digitali, rendendo possibile una gestione e una valutazione integrata dei fornitori, i cui processi devono rispecchiare lo standard richiesto.
5
Le “parole chiave” della digitalizzazione aziendale
Di seguito riportiamo alcune parole chiave che rappresentano i pilastri della digitalizzazione in ambito aziendale e che guidano concretamente il modo in cui RIMSA applica l’innovazione digitale all’interno dei propri processi, valorizzando efficienza, sostenibilità e responsabilità.
1. CRM (Customer Relationship Management) ↓
Il CRM (Customer Relationship Management) è lo strumento che permette a un’azienda di gestire i rapporti con i clienti e i potenziali acquirenti. In un contesto Industria 4.0, il CRM diventa il punto di raccordo tra le esigenze del mercato e le varie funzioni aziendali, consentendo di sviluppare offerte personalizzate, migliorare il servizio di assistenza e ottimizzare le azioni di marketing.
Dal punto di vista tecnologico, un CRM moderno non si limita a gestire anagrafiche clienti o opportunità di vendita: integra dati da molteplici canali (email, social media, e-commerce), fornendo una visione a 360° del cliente. In questo modo, il team commerciale o il servizio post-vendita può accedere a informazioni aggiornate in tempo reale, offrendo risposte puntuali e un’esperienza coerente.
La digitalizzazione del CRM si esprime anche attraverso funzionalità di automazione e analisi dei dati, che permettono di identificare pattern di acquisto, segmentare la clientela, pianificare campagne mirate. Il sistema può interagire con altre piattaforme, come ERP o PLM, consentendo di verificare rapidamente la disponibilità di prodotti, gestire la personalizzazione di un ordine o monitorare la produzione di un articolo su misura.
La verticalizzazione dei processi, grazie al CRM, significa ridurre la distanza tra chi si interfaccia col mercato e chi produce fisicamente il bene. Quando un cliente invia una richiesta, è possibile verificare in pochi clic lo stato di avanzamento dell’ordine o di un eventuale reclamo, collegando tale informazione anche al sistema di gestione qualità.
In sintesi, il CRM fornisce un vero e proprio “cruscotto relazionale” che dà centralità all’esperienza del cliente e, di riflesso, sostiene la reputazione aziendale. In una logica di industria connessa, infatti, la soddisfazione del cliente diventa una leva competitiva essenziale, raggiungibile solo con strumenti di gestione integrata e team orientati alla collaborazione.
2. ERP (Enterprise Resource Planning) ↓
L’ERP (Enterprise Resource Planning) è il cuore pulsante di molte aziende, poiché coordina tutti i flussi informativi di carattere economico e amministrativo. Al suo interno, si gestiscono ordini, fatturazione, contabilità, anagrafiche di prodotto e di magazzino, pianificazione della produzione e molto altro. In un contesto di Industria 4.0, l’ERP diventa un nodo fondamentale di integrazione, poiché riceve e trasmette dati a CRM, MRP, PLM e a qualsiasi altro software aziendale.
Una delle principali evoluzioni dell’ERP nell’era digitale è la modularità: le aziende possono scegliere i moduli più adatti alle proprie esigenze, integrandoli via API o connettori standard. In questo modo, si evitano duplicazioni di dati e si garantisce l’allineamento costante delle informazioni. Pensiamo, ad esempio, a un ordine cliente che, appena inserito nel CRM, viene automaticamente trasmesso all’ERP per la verifica delle scorte e la generazione della distinta base, senza alcun passaggio manuale.
Un ERP ben strutturato fornisce dati in tempo reale sulla situazione economica-finanziaria e di magazzino, migliorando la capacità di prendere decisioni basate su KPI solidi. Inoltre, grazie all’analisi predittiva, diventa possibile stimare i flussi di cassa futuri, pianificare investimenti o analizzare la redditività di determinati progetti.
Nel contesto di RIMSA, l’ERP è il perno che collega ufficio acquisti, magazzino e reparto produzione: quando un ordine di produzione viene lanciato, l’ERP notifica il magazzino delle materie prime da prelevare e, contemporaneamente, aggiorna i fabbisogni futuri in base alle previsioni di vendita. In caso di modifiche al disegno di un componente, l’ERP interagisce con il PLM e l’MRP, riflettendo in tempo reale le nuove specifiche.
Con l’adozione di un ERP integrato, si ottiene dunque controllo, trasparenza e rapidità di esecuzione, riducendo gli errori dovuti a procedure manuali o a mancate comunicazioni tra reparti, elementi chiave per un’azienda che punta alla massima efficienza.
3. MRP (Material Requirements Planning) ↓
Il MRP (Material Requirements Planning) è il sistema che consente di calcolare i fabbisogni di materiali e componenti in base ai piani di produzione e alle previsioni di vendita. Si tratta di uno strumento cruciale in ottica Industria 4.0, poiché permette un controllo rigoroso delle scorte, evitando surplus inutili e carenze che bloccano la linea.
A livello funzionale, il MRP legge gli ordini di produzione e la distinta base di ogni articolo. Incrociando queste informazioni con i livelli di magazzino, determina automaticamente le quantità di materie prime e semilavorati da acquistare o produrre. In un’azienda connessa, questo processo è completamente integrato con l’ERP, il PLM e i moduli di produzione, eliminando passaggi manuali e limitando errori.
Inoltre, un MRP evoluto gestisce anche i tempi di approvvigionamento, i lotti minimi e le scorte di sicurezza, contribuendo a ottimizzare le strategie di acquisto e di produzione. Se, per esempio, un componente ha un lead time di 4 settimane, il sistema pianifica l’ordine in anticipo, prevenendo ritardi. La verticalizzazione dei processi, quando un’azienda decide di internalizzare alcune lavorazioni, richiede che il MRP sia in grado di gestire anche la disponibilità di macchinari e operatori, non solo quella dei materiali.
Per RIMSA, il MRP assume un ruolo centrale nella riduzione degli sprechi e nel raggiungimento del JIT (Just In Time): quando un ordine entra nel sistema, il MRP coordina i vari reparti, stabilendo quali componenti vanno prodotti internamente e quali acquistati da fornitori, e in quali tempistiche. Se un disegno subisce variazioni, il MRP aggiorna la distinta base e le specifiche di approvvigionamento, comunicando automaticamente le modifiche al magazzino e all’ufficio acquisti.
In definitiva, il MRP offre visibilità, pianificazione integrata e tracciabilità, elementi imprescindibili per una gestione oculata di risorse e scorte in un contesto industriale ad alto tasso di dinamicità.
4. PLM (Product Lifecycle Management) ↓
Il PLM (Product Lifecycle Management) è la piattaforma che gestisce l’intero ciclo di vita di un prodotto, dalla fase di ideazione alla progettazione, produzione, distribuzione e dismissione. In un contesto Industria 4.0, il PLM diventa una sorta di “deposito centrale” per tutte le informazioni e revisioni che riguardano i prodotti dell’azienda.
A livello pratico, il PLM conserva i modelli 3D, le distinte base, le specifiche tecniche, la documentazione di test e certificazioni. Qualunque modifica a un disegno, a una quota o a un materiale viene registrata in tempo reale, generando una nuova revisione che si propaga agli altri sistemi integrati, come ERP e MRP. Ciò consente di evitare errori tipici della comunicazione analogica, come file obsoleti o indicazioni poco chiare.
Un PLM moderno prevede anche funzionalità di collaborazione e workflow management, permettendo a progettisti, responsabili qualità, produzione e altre funzioni di cooperare su un unico progetto. Per esempio, il reparto qualità può aggiungere tolleranze e piani di controllo direttamente sul modello 3D, mentre i progettisti ricevono notifiche sulle richieste di modifica.
Nel caso di RIMSA, la customizzazione del PLM è stata studiata per integrare i dati di QA, CAM e MRP: se un disegnatore modifica un disegno, il software avvisa immediatamente il responsabile CAM, il quale aggiorna il programma macchina. Se il programma macchina non corrisponde alla revisione del disegno, la macchina utensile blocca la lavorazione, prevenendo difetti di produzione.
Questo livello di interconnessione e tracciabilità consente di creare un vero e proprio “passaporto digitale” di ogni prodotto, in cui sono memorizzate tutte le informazioni critiche, dalle specifiche di design ai collaudi finali, offrendo un notevole vantaggio competitivo in termini di qualità e servizio al cliente.
5. Cloud ↓
Il Cloud rappresenta oggi l’infrastruttura abilitante per l’Industria 4.0. Anziché mantenere server fisici all’interno dell’azienda, il cloud consente di sfruttare risorse informatiche in remoto, garantendo maggiore scalabilità, affidabilità e sicurezza. Le piattaforme in cloud rendono anche più semplice l’interconnessione tra i vari reparti e con i fornitori, consentendo l’accesso ai dati da qualunque luogo e dispositivo, a patto che vi sia una connessione Internet stabile.
Per un’azienda come RIMSA, il passaggio al cloud significa poter integrare i diversi sistemi (CRM, ERP, MRP, PLM, LMS) in un ambiente unificato, senza doversi preoccupare eccessivamente delle infrastrutture hardware. Questo approccio facilita gli aggiornamenti software, che avvengono in modo automatico e trasparente per gli utenti finali, e garantisce backup e piani di disaster recovery più solidi rispetto alle soluzioni on-premise.
Un ulteriore vantaggio del cloud è l’elasticità: l’azienda può incrementare o ridurre la potenza di calcolo o lo spazio di archiviazione a seconda delle necessità, ad esempio in caso di picchi di lavoro stagionali o di progetti straordinari. Sul versante economico, i costi si trasformano da investimenti iniziali (CAPEX) a spese operative (OPEX), offrendo maggiore flessibilità nella gestione finanziaria.
Da un punto di vista collaborativo, il cloud consente al personale di condividere rapidamente documenti, disegni e report con colleghi, partner o clienti, potendo anche lavorare in simultanea su uno stesso file. Nel caso di implementazioni IoT (Internet of Things), i dati generati da sensori e macchinari vengono inviati in tempo reale ai server remoti, dove algoritmi di analisi predittiva possono elaborare modelli complessi.
In sintesi, l’adozione del cloud non è più un lusso, ma un tassello fondamentale di qualsiasi strategia Industria 4.0, poiché rende la digitalizzazione più agile, economica e sicura.
6. Verticalizzazione dei processi ↓
La verticalizzazione dei processi, in ottica Industria 4.0, consiste nel portare internamente alcune fasi di produzione o sviluppo, così da ridurre la dipendenza da fornitori esterni e aumentare il controllo su tempistiche, costi e qualità. Non si tratta di “chiudere” la filiera, ma di strutturarla in modo che il valore aggiunto rimanga in azienda, e che i partner esterni siano integrati digitalmente tanto quanto i reparti interni.
In RIMSA, la verticalizzazione si è tradotta nell’internalizzazione di diverse lavorazioni, a partire dalla progettazione fino alla verniciatura e al collaudo, integrando macchine utensili e software gestionali in un’unica piattaforma informatica. Questa scelta permette di accorciare la catena logistica, riducendo tempi di consegna e rendendo l’azienda meno vulnerabile a eventuali ritardi o inefficienze di terzi.
Un altro vantaggio della verticalizzazione è la tracciabilità end-to-end: gestendo direttamente ogni passaggio, si dispone di una visione globale del processo. Per esempio, quando un componente deve subire una fase di lavorazione speciale (tornitura, fresatura, verniciatura), l’azienda può programmare la produzione in MRP, far eseguire l’operazione su un macchinario CNC interconnesso e registrare i risultati di collaudo nel PLM, senza perdere continuità informativa.
Ciò migliora anche la qualità, perché i test e le verifiche possono essere effettuati in loco a più riprese, integrandoli direttamente nell’iter produttivo. Questa strategia non esclude la collaborazione con fornitori esterni, ma li rende parte di un sistema condiviso, in cui vige un controllo puntuale dei requisiti e delle specifiche.
In definitiva, la verticalizzazione in chiave 4.0 massimizza l’efficienza, la trasparenza e la capacità di adattarsi alle richieste del mercato, favorendo un rapporto più diretto tra progettazione, produzione e cliente finale.
7. Dall’ufficio tecnico alla macchina: Disegno 3D, QA e CAM ↓
Uno degli esempi più eclatanti di integrazione Industria 4.0 è la comunicazione fluida tra progettazione, controllo qualità e reparti produttivi. Immaginiamo lo scenario in cui il disegnatore di RIMSA realizzi un modello 3D di un nuovo componente. Questo file, salvato nel sistema PLM, diventa subito visibile al responsabile qualità, il quale aggiunge tolleranze e parametri di controllo in varie fasi (accettazione del materiale, pre-lavorazione, test finali), il tutto sullo stesso disegno digitale.
A questo punto, il PLM notifica automaticamente l’MRP, che aggiorna i fabbisogni di materiali e i cicli di lavorazione. Se il prodotto richiede una fresatura CNC, il responsabile CAM elabora il programma macchina, assicurandosi che la revisione del disegno e quella del CAM coincidano. Qui entra in gioco l’interazione uomo-macchina: la fresatrice attinge il programma direttamente dal PLM. Se ci fosse una discrepanza tra il disegno revisionato e il programma CAM, la macchina si bloccherebbe, segnalando un errore di versione. Solo quando il CAM viene allineato, la produzione prosegue.
Contemporaneamente, il responsabile qualità può decidere quali misure debbano essere verificate in linea, caricando i valori e le tolleranze nei sistemi di misura connessi. Così, gli operatori non trascrivono più a mano le quote, evitano errori e, soprattutto, lavorano sempre sui dati aggiornati.
Il vantaggio di questa catena digitale integrata è evidente: riduzione drastica degli errori, maggiore velocità nell’implementare revisioni e aggiornamenti, e un controllo qualità esteso all’intero ciclo, non relegato a un controllo finale. Questo “flusso continuo” fra disegno, QA e reparti produttivi incarna l’idea di un ecosistema 4.0 in cui ogni fase parla la stessa “lingua digitale” e in cui la tracciabilità diventa un asset fondamentale per la competitività e l’innovazione continua.
8. Passaporto digitale, KPI e JIT ↓
In un’azienda che adotta i principi 4.0, ogni pezzo o lotto viene “tracciato” digitalmente lungo tutte le fasi di produzione e collaudo. Questo crea un vero e proprio “passaporto digitale”: quando si arriva al prodotto finito con una determinata matricola, si può risalire a tutti i componenti usati, ai seriali univoci delle parti interne, ai test effettuati e ai risultati ottenuti. In RIMSA, per esempio, ogni volta che un componente subisce una trasformazione, gli viene assegnato un seriale: se successivamente verrà assemblato in un prodotto più complesso, quel seriale sarà inglobato nella matricola finale, ma rimarrà sempre consultabile a ritroso.
Grazie a questa tracciabilità, non solo si facilita la manutenzione post-vendita (sostituendo esattamente la parte difettosa con una identica per parametri e prestazioni), ma si migliora la qualità del prodotto. Infatti, eventuali anomalie vengono individuate e circoscritte velocemente, riducendo l’impatto sui lotti futuri. Il passaporto digitale, inoltre, rappresenta un elemento di trasparenza fondamentale da presentare a clienti e partner.
Sul fronte gestionale, la raccolta di dati in tempo reale consente di definire KPI (Key Performance Indicator) chiari: tempi di produzione, tempi di setup, numero di pezzi difettosi, consumi energetici, e molto altro. Monitorare queste metriche permette di intervenire tempestivamente, correggere eventuali inefficienze e analizzare i trend per un miglioramento continuo.
Infine, l’approccio Just In Time (JIT) beneficia enormemente di queste tecnologie: il sistema pianifica in modo preciso la produzione sulla base delle reali esigenze e dei cicli di lavoro, evitando accumuli di magazzino e riducendo gli sprechi. Se l’MRP segnala che è giunto il momento di lanciare la produzione, i reparti sanno esattamente quali materiali prelevare e quando farlo, mentre il sistema informatico gestisce automaticamente le priorità in base agli ordini effettivi e alle previsioni di vendita.
In sintesi, passaporto digitale, KPI e JIT formano un triangolo virtuoso di controllo, miglioramento e rapida reattività ai mutamenti del mercato, rendendo l’azienda davvero resiliente e competitiva.
6
Conclusioni: la digitalizzazione come cultura aziendale
Il percorso di trasformazione digitale di RIMSA dimostra come l’Industria 4.0 non sia soltanto una questione di tecnologie all’avanguardia, ma anche di approccio culturale.
Dalla progettazione alla produzione, dalla logistica al controllo qualità, ogni funzione aziendale deve cooperare in modo fluido, basandosi su una piattaforma digitale comune e su processi condivisi. In tal senso, la formazione del personale e la spinta verso la collaborazione diventano fattori determinanti per il successo.
I vantaggi, del resto, sono tangibili: maggiore controllo, riduzione dei costi e degli sprechi, efficienza energetica, trasparenza e tracciabilità su ogni passaggio. Sul piano umano, un ambiente di lavoro digitale offre opportunità di crescita, stimola la curiosità e accresce il coinvolgimento delle persone. L’integrazione dei dati e l’interconnessione delle macchine consentono di migliorare la qualità in modo sistematico, garantendo al cliente finale un prodotto affidabile, ben tracciato e in linea con i più alti standard.
Alla fine, la digitalizzazione non è un traguardo, ma un processo in continuo divenire. Per rimanere competitivi, le aziende devono aggiornare costantemente i loro sistemi informativi e formare il personale sulle nuove tecnologie, mantenendo sempre al centro l’innovazione e la qualità. RIMSA, con il suo esempio, mostra che anche le PMI possono intraprendere con successo questa strada, affermandosi come leader di settore e promotrici di una nuova cultura industriale.