Embracing a sustainable industrial model means adopting production and management processes that minimize environmental impact, optimize resource usage, and foster long-term social and economic well-being. Always anticipating the future, RIMSA initiated a corporate digitalization journey in 2000, which now culminates in an integrated management system that responsibly and sustainably connects people and machinery.
RIMSA Model
Sustainable Industry
Digitalization: From an Applied Tool to Corporate Culture
How Industry 4.0 principles are reshaping processes, technology, and methodologies in a fully integrated production environment.
In the realm of technological transformation and shifting production models, RIMSA began its journey toward 4.0 digitalization back in 2000—well ahead of the curve. Over time, introducing cutting-edge operational tools gradually became embedded in the company’s values and processes, ultimately evolving into a genuinely forward-thinking corporate culture that is sustainable, responsible, and future-oriented.
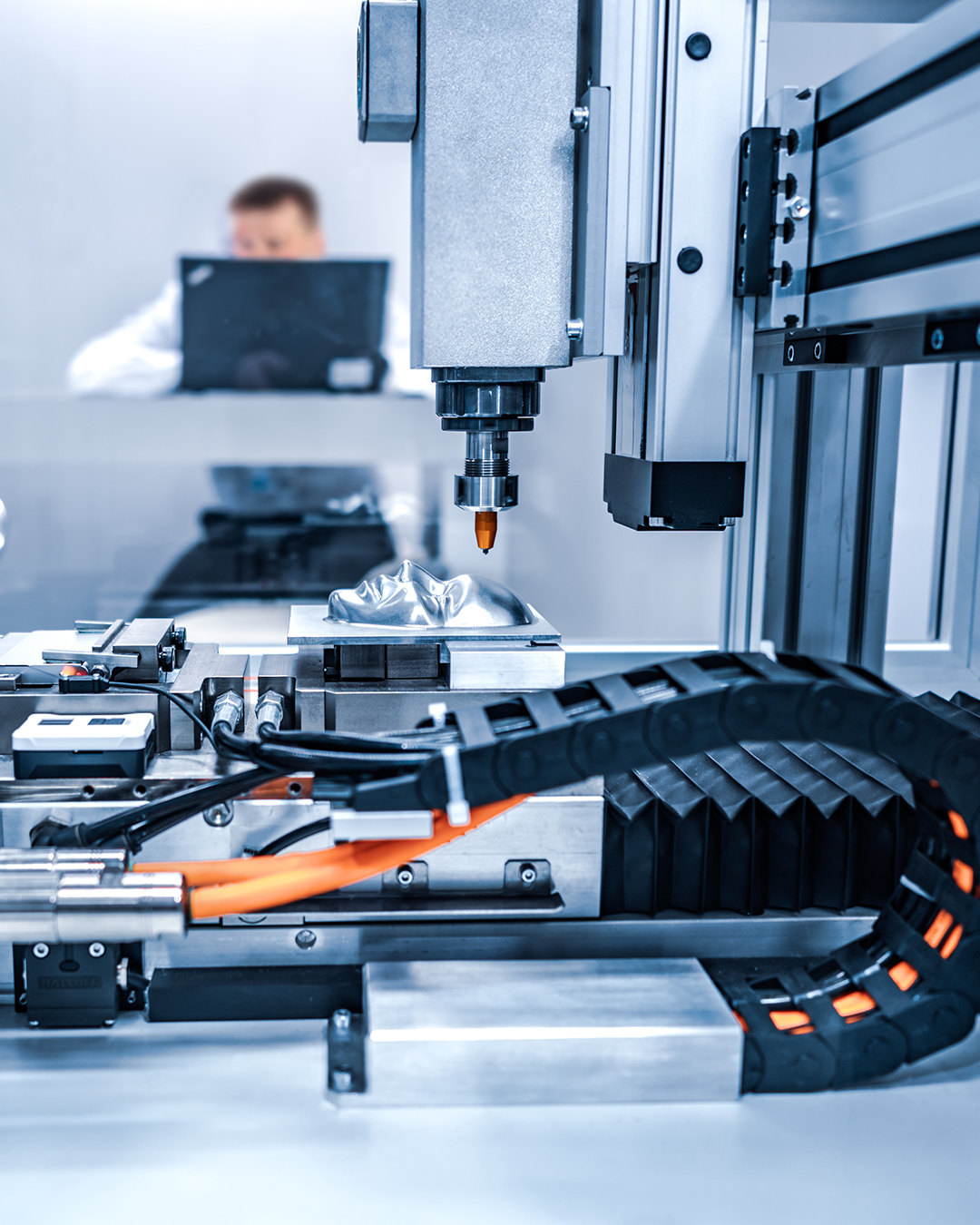
1
Introduction to Industry 4.0
Industry 4.0 marks a profound shift in how companies design their workflows, manage information, and shape their organizational culture.
Rather than focusing primarily on mechanical automation and process control as in earlier eras, today’s emphasis centers on digital connectivity—linking machines, software, and human teams into a single, intelligent ecosystem. Several foundational ideas define Industry 4.0: digitalization of workflows, interconnection among systems and devices, software integration at every level, real-time data analysis, predictive insights, and vertical integration aimed at streamlining supply chains. RIMSA stands out as a compelling example of how a medium-sized company can successfully embark on a comprehensive digital transformation journey, revolutionizing its operating model step by step.
2
Core Principles of Industry 4.0
The fundamentals of Industry 4.0 are based on key concepts that define the evolution of production processes towards an increasingly connected, automated and intelligent model.
Before to venture on the analysis of Rimsa as an example of digitalization, some definitions are offered. Click to discover more.
Digitalization
Digitalization involves reimagining business processes through digital technologies, not merely replacing paper with electronic files. It’s a chance to leverage up-to-the-minute data and advanced software, fostering smoother communication across different departments. At RIMSA, digitalization means having interconnected project workflows, streamlined production cycles, and unified logistics data—all synchronized through integrated platforms.
Interconnection
The true power of Industry 4.0 lies in the connectivity that links sensors, machines, software, and operators within a smart network. Every element supplies and retrieves data in real time, enabling faster, data-driven decision-making. For example, if a painting line detects a deviation in material usage, it immediately updates the ERP or MRP system, prompting timely interventions. The design, quality, and manufacturing teams stay perpetually in sync, which boosts overall efficiency.
Software Integration
Full-fledged software integration creates a “digital ecosystem” where CRM, ERP, MRP, PLM, CAM, and other systems seamlessly collaborate. This approach eliminates siloed data and improves cross-department alignment. At RIMSA, a 3D model designed in CAD and uploaded to the PLM can be instantly accessed by Quality Assurance (QA) while simultaneously informing the MRP system about required materials and process updates.
Data Analysis
Data is the cornerstone of Industry 4.0. Collecting, processing, and interpreting information in real time provides the strategic insights needed for agile and evidence-based decisions. Whether focusing on production statistics, sales figures, or inventory trends, data becomes the backbone of Key Performance Indicators (KPIs) that reveal operational strengths and areas for improvement.
Predictive Analytics
Going beyond traditional reporting, Industry 4.0 embraces predictive analytics, helping companies anticipate and address future scenarios. Through machine learning algorithms or statistical models, RIMSA can forecast machine maintenance needs, detect likely spikes in demand, and plan resource allocation accordingly. This approach minimizes downtime, optimizes stock levels, and drives a proactive, rather than reactive, strategy.
Vertical Integration
Vertical integration (or shortening the supply chain) involves bringing critical production or development stages in-house to reduce reliance on external vendors and ensure direct control over quality and lead times. In an Industry 4.0 context, vertical integration isn’t just “do everything internally”; it’s about coupling in-house processes with digital systems that guarantee consistent standards and fast turnaround. RIMSA, for instance, internalizes certain phases but also demands transparent data and quality assurance reports from its key suppliers to maintain unified standards across the board.
3
Key Advantages of Industry 4.0
A fully digitised and integrated environment makes it possible to know at all times where materials are, what stage a process is at and what tests have been carried out on a particular component. In this way, the company not only reduces errors and rework, but can intervene promptly in the event of anomalies.
Cost and Waste Reduction
Digital workflows streamline operations by removing redundant steps and minimizing manual data re-entry. Better planning also leads to optimal resource usage, from raw materials to staffing. Through automated MRP scheduling, RIMSA curbs both overstocking and the production of goods that no longer match market demand. Fewer mistakes and faster interventions translate into lower overall costs.
The Digital Passport
At RIMSA, every part produced gets a digital passport, where processing data, component serial numbers, tests performed and results are collected. If a component is found to be non-conforming, it is immediately traced back to its origin, improving time-to-resolution.
Reducing costs and waste
Digitalisation means streamlining processes by eliminating unnecessary steps and reducing duplication of data or documents. In addition, better planning makes it possible to optimise the use of resources (raw materials, time, personnel). In the case of RIMSA, timely control of production cycles and synchronised warehouse management through MRP reduce waste both in terms of overstocking and production that is no longer required by the market.
Improved Energy Efficiency
Industry 4.0 makes sustainability a built-in objective rather than an afterthought. Real-time monitoring of energy usage and the deployment of smart devices (LED lighting, modern CNC machines) allow more precise control. If there is a lull in production, for instance, certain systems can automatically scale down power consumption. Tracking carbon emissions also becomes feasible, enabling robust environmental strategies alongside energy savings.
Social Sustainability
Digital work environments aren’t just more efficient; they also tend to be more engaging for employees. Intuitive software tools (from tablets to user-friendly dashboards) boost involvement and transparency, while continuous learning platforms encourage skill development. RIMSA notably invests in staff training—enabling workers to operate different machines and processes—thereby facilitating mobility and creating an enriched workforce that can adapt to changing roles and responsibilities.
Superior Quality
Quality assurance thrives in a connected ecosystem where every process is tracked in real time. From raw materials intake to final product inspection, each step can be linked to the relevant digital file or component serial. Thanks to integration between PLM, QA, and production systems, data stays consistently up to date and machines won’t proceed with out-of-date or mismatched designs.
4
Digital Transformation in Practice: RIMSA’s Model
RIMSA, a specialized company with a strong focus on high-quality professional lighting solutions (among other areas), embarked on a progressive digital transformation affecting every department. This shift didn’t happen overnight: it required a clear vision, a roadmap for software and machinery investment, and a commitment to ongoing training.
From Technical Office to Final Production
The CAD designer at RIMSA creates a 3D model of a new part, uploading it to the PLM system for immediate access by QA, procurement, and production. Thanks to tailored software features, the QA manager can then embed critical tolerances and inspection points (e.g., upon material intake, pre-production checks, and post-assembly) right into that same design file. The MRP pulls this data from the PLM and auto-updates relevant control plans and measurement devices, eliminating manual entry and reducing errors.
Meanwhile, the production manager defines the manufacturing workflow through an intuitive interface—assigning materials, components, and the necessary machinery to each phase. The time-and-methods specialist then sets estimated production times, cross-checking them with real output data for constant process refinement. This continuous flow of information ensures that production cycles align tightly with real-world conditions, boosting accuracy and reactivity.
Human–Machine Interaction and CAM Control
Industry 4.0 is about direct, user-friendly interaction between operators, machinery, and integrated systems. At RIMSA, machines automatically download their programs from the central PLM repository. If the designer updates a drawing in CAD, the machine verifies whether the CAM program is in sync with the new revision. If any mismatch is detected, production halts until the CAM manager releases the correct version—a strong safeguard against manufacturing errors caused by outdated files.
Internal Logistics, Bills of Materials, and Warehouse Management
Digitalization extends into logistics. The bill of materials (BOM) for each product covers not only required parts but also the specific production stages. Once a production phase is triggered, the warehouse receives a system-generated pick list indicating exact quantities and timing. This eliminates guesswork, minimizes downtime, and ensures operators have the right components at the right moment.
“Smart” Workstations and Continuous Training
Each production operator at RIMSA is equipped with a tablet for real-time access to digital drawings (in a viewer mode), assembly instructions, and on-hand inventory. If an operator has questions, they can jump onto the corporate LMS (Learning Management System) for step-by-step guidance on assembly or to learn new machine techniques. This structure not only enhances operator expertise but also encourages cross-training. Employees can explore and develop new skills, potentially transitioning into different roles—a clear sign of a modern and dynamic work environment.
Total Traceability and the Digital Passport
Quality checks, machine processes, and test reports are stored and bound to a specific lot number or serial ID, creating a seamless audit trail. Each significant transformation step generates a unique serial number for that component. When the final product is assembled, those serials become part of its overarching ID. Anyone with the final product’s serial can access its complete history of tests, results, and component details. This approach simplifies post-sales service and ensures quick fixes with the exact specifications used in the original build.
KPI Tracking and JIT Strategies
Because data seamlessly flows throughout the company, RIMSA can track real-time KPIs such as production rates, downtime, operator performance, and non-compliance instances. Just In Time (JIT) gains traction: the system only schedules production when needed, drastically reducing excess inventory and accelerating lead times. If a job is initiated, each department and station knows its exact role and the necessary resources, thanks to continuously refreshed data and scheduling.
Supplier Collaboration
Quality extends beyond an individual company’s walls. RIMSA expects its suppliers to mirror its commitment to transparency and quality management. For each externally sourced part, suppliers provide comprehensive digital reports, ensuring reliability. This external data is integrated into RIMSA’s systems, forming a single, cohesive source of truth about parts, processes, and test outcomes.
5
The ‘keywords’ of corporate digitalization
Below are a few keywords that represent the pillars of digitisation in the business environment and that concretely guide the way RIMSA applies digital innovation within its processes, enhancing efficiency, sustainability and responsibility.
1. CRM (Customer Relationship Management) ↓
CRM (Customer Relationship Management) is the tool that enables a company to manage relationships with customers and prospects. In an Industry 4.0 context, CRM becomes the point of connection between market needs and the various business functions, making it possible to develop customised offers, improve customer service and optimise marketing actions.
From a technological point of view, a modern CRM does not only manage customer master data or sales opportunities: it integrates data from multiple channels (email, social media, e-commerce), providing a 360° view of the customer. In this way, the sales team or after-sales service can access up-to-date information in real time, offering timely responses and a consistent experience.
The digitalization of CRM is also expressed through automation and data analysis functionalities, which make it possible to identify purchasing patterns, segment customers, and plan targeted campaigns. The system can interact with other platforms, such as ERP or PLM, allowing to quickly check product availability, manage the customisation of an order or monitor the production of a customised item.
The verticalisation of processes, thanks to CRM, means reducing the distance between those who interface with the market and those who physically produce the good. When a customer sends in a request, it is possible to check the status of the order or a possible complaint in a few clicks, linking this information also to the quality management system.
In summary, CRM provides a true ‘relational dashboard’ that gives centrality to the customer experience and, by extension, supports the company’s reputation. Indeed, in a connected industry logic, customer satisfaction becomes an essential competitive lever that can only be achieved with integrated management tools and collaboration-oriented teams.
2. ERP (Enterprise Resource Planning) ↓
ERP (Enterprise Resource Planning) is the beating heart of many companies, as it coordinates all economic and administrative information flows. Within it, orders, invoicing, accounting, product and warehouse master data, production planning and much more are managed. In an Industry 4.0 context, the ERP becomes a fundamental integration node, as it receives and transmits data to CRM, MRP, PLM and any other business software.
One of the main evolutions of ERP in the digital era is modularity: companies can choose the modules best suited to their needs, integrating them via APIs or standard connectors. In this way, duplication of data is avoided and constant alignment of information is guaranteed. Let’s think, for example, of a customer order that, as soon as it is entered into CRM, is automatically transmitted to the ERP for stock verification and the generation of the bill of materials, without any manual steps.
A well-structured ERP provides real-time data on the financial and stock situation, improving the ability to make decisions based on solid KPIs. Moreover, thanks to predictive analysis, it becomes possible to estimate future cash flows, plan investments or analyse the profitability of certain projects.
In the context of RIMSA, the ERP is the pivot that connects the purchasing department, warehouse and production department: when a production order is launched, the ERP notifies the stock of raw materials to be picked and, at the same time, updates future requirements based on sales forecasts. In the event of changes to a component design, the ERP interacts with the PLM and MRP, reflecting the new specifications in real time.
With the adoption of an integrated ERP, control, transparency and speed of execution are thus achieved, reducing errors due to manual procedures or lack of communication between departments, key elements for a company aiming for maximum efficiency.
3. MRP (Material Requirements Planning) ↓
MRP (Material Requirements Planning) is the system for calculating material and component requirements based on production plans and sales forecasts. It is a crucial tool in the context of Industry 4.0, as it allows strict stock control, avoiding unnecessary surpluses and shortages that block the line.
At the functional level, the MRP reads the production orders and the bill of materials for each article. Cross-referencing this information with stock levels, it automatically determines the quantities of raw materials and semi-finished products to be purchased or produced. In a connected company, this process is fully integrated with the ERP, PLM and production modules, eliminating manual steps and limiting errors.
In addition, an advanced MRP also manages procurement times, minimum batches and safety stocks, helping to optimise purchasing and production strategies. If, for example, a component has a lead time of 4 weeks, the system schedules the order in advance, preventing delays. The verticalisation of processes, when a company decides to internalise certain processes, requires that the MRP is also able to manage the availability of machinery and operators, not only that of materials.
For RIMSA, the MRP assumes a central role in reducing waste and achieving JIT (Just In Time): when an order enters the system, the MRP coordinates the various departments, establishing which components are to be produced in-house and which are to be purchased from suppliers, and in what timeframe. If a drawing changes, the MRP updates the bill of materials and procurement specifications, automatically communicating the changes to the warehouse and purchasing department.
Ultimately, the MRP offers visibility, integrated planning and traceability, which are essential elements for the prudent management of resources and stocks in a highly dynamic industrial context.
4. PLM (Product Lifecycle Management) ↓
PLM (Product Lifecycle Management) is the platform that manages the entire life cycle of a product, from the ideation phase to design, production, distribution and disposal. In an Industry 4.0 context, PLM becomes a sort of “central repository” for all the information and revisions regarding the company’s products.
On a practical level, PLM stores 3D models, bills of materials, technical specifications, test documentation and certifications. Any change to a drawing, a dimension or a material is recorded in real time, generating a new revision that propagates to other integrated systems, such as ERP and MRP. This helps avoid errors typical of analog communication, such as obsolete files or unclear indications.
A modern PLM also includes collaboration and workflow management features, allowing designers, quality managers, production and other functions to collaborate on a single project. For example, the quality department can add tolerances and control plans directly on the 3D model, while designers receive notifications about change requests. In the case of RIMSA, the PLM customization was designed to integrate QA, CAM and MRP data: if a designer modifies a drawing, the software immediately notifies the CAM manager, who updates the machine program. If the machine program does not match the revision of the drawing, the machine tool stops processing, preventing production defects. This level of interconnection and traceability allows for the creation of a true “digital passport” for each product, in which all critical information is stored, from design specifications to final testing, offering a significant competitive advantage in terms of quality and customer service.
5. Cloud ↓
The Cloud is today’s enabling infrastructure for Industry 4.0. Instead of maintaining physical servers within the company, the cloud allows remote computing resources to be exploited, ensuring greater scalability, reliability and security. Cloud platforms also make it easier to interconnect between departments and with suppliers, allowing access to data from anywhere and on any device, as long as there is a stable Internet connection.
For a company like RIMSA, the move to the cloud means being able to integrate different systems (CRM, ERP, MRP, PLM, LMS) in a unified environment, without having to worry too much about hardware infrastructure. This approach facilitates software updates, which take place automatically and transparently for end users, and ensures more robust backups and disaster recovery plans than on-premise solutions.
A further advantage of the cloud is its elasticity: the company can increase or reduce computing power or storage space as required, e.g. for seasonal work peaks or extraordinary projects. On the economic side, costs are transformed from initial investment (CAPEX) to operating expenditure (OPEX), offering greater flexibility in financial management.
From a collaborative point of view, the cloud allows staff to quickly share documents, drawings and reports with colleagues, partners or customers, even working simultaneously on the same file. In the case of IoT (Internet of Things) deployments, data generated by sensors and machines are sent in real time to remote servers, where predictive analysis algorithms can process complex patterns.
In summary, the adoption of the cloud is no longer a luxury, but a fundamental building block of any Industry 4.0 strategy, as it makes digitisation more agile, economical and secure.
6. Processes verticalisation ↓
Process verticalisation, in the context of Industry 4.0, consists of bringing certain production or development steps in-house, so as to reduce dependence on external suppliers and increase control over timing, costs and quality. It is not a matter of ‘closing’ the supply chain, but of structuring it in such a way that the added value remains in the company, and external partners are as digitally integrated as internal departments.
At RIMSA, verticalisation has translated into the internalisation of various processes, from design to painting and testing, integrating machine tools and management software into a single IT platform. This choice makes it possible to shorten the logistics chain, reducing delivery times and making the company less vulnerable to delays or inefficiencies of third parties.
Another advantage of verticalisation is end-to-end traceability: by directly managing each step, one has a global view of the process. For example, when a component has to undergo a special machining step (turning, milling, painting), the company can schedule the production in MRP, have the operation performed on an interconnected CNC machine and record the test results in PLM, without losing information continuity.
This also improves quality, because tests and inspections can be carried out on-site in several stages, integrating them directly into the production process. This strategy does not exclude collaboration with external suppliers, but makes them part of a shared system in which requirements and specifications are closely monitored.
Ultimately, verticalisation in 4.0 maximises efficiency, transparency and the ability to adapt to market demands, fostering a more direct relationship between design, production and the end customer.
7. From engineering to machine: 3D, QA and CAM ↓
One of the most striking examples of Industry 4.0 integration is the seamless communication between design, quality control and production departments. Let’s imagine the scenario in which the RIMSA designer creates a 3D model of a new component. This file, saved in the PLM system, immediately becomes visible to the quality manager, who adds tolerances and control parameters at various stages (material acceptance, pre-processing, final tests), all on the same digital drawing. At this point, the PLM automatically notifies the MRP, which updates the material requirements and processing cycles. If the product requires CNC milling, the CAM manager processes the machine program, ensuring that the revision of the drawing and that of the CAM match. This is where human-machine interaction comes into play: the milling machine draws the program directly from the PLM. If there were a discrepancy between the revised drawing and the CAM program, the machine would block, signaling a version error. Only when the CAM is aligned, production continues.
At the same time, the quality manager can decide which measurements need to be verified online, loading the values and tolerances into the connected measurement systems. In this way, operators no longer transcribe measurements by hand, avoid errors and, above all, always work on updated data. The advantage of this integrated digital chain is clear: drastic reduction of errors, greater speed in implementing revisions and updates, and quality control extended to the entire cycle, not relegated to a final check. This “continuous flow” between design, QA and production departments embodies the idea of a 4.0 ecosystem in which each phase speaks the same “digital language” and in which traceability becomes a fundamental asset for competitiveness and continuous innovation.
8. Digital passport, KPI and JIT ↓
In a company that adopts 4.0 principles, each piece or batch is digitally “tracked” throughout all production and testing phases. This creates a true “digital passport”: when you get to the finished product with a specific serial number, you can trace all the components used, the unique serial numbers of the internal parts, the tests performed and the results obtained. In RIMSA, for example, every time a component undergoes a transformation, it is assigned a serial number: if it is subsequently assembled into a more complex product, that serial number will be incorporated into the final serial number, but will always remain consultable backwards.
Thanks to this traceability, not only is post-sale maintenance facilitated (by replacing the defective part with an identical one in terms of parameters and performance), but the quality of the product is improved. In fact, any anomalies are quickly identified and limited, reducing the impact on future batches. The digital passport also represents a fundamental element of transparency to present to customers and partners. On the management front, the collection of data in real time allows you to define clear KPIs (Key Performance Indicators): production times, setup times, number of defective pieces, energy consumption, and much more. Monitoring these metrics allows you to intervene promptly, correct any inefficiencies and analyze trends for continuous improvement.
Finally, the Just In Time (JIT) approach benefits greatly from these technologies: the system precisely plans production based on real needs and work cycles, avoiding inventory build-ups and reducing waste. If the MRP signals that it is time to launch production, the departments know exactly which materials to pick and when, while the IT system automatically manages priorities based on actual orders and sales forecasts. In short, digital passport, KPIs and JIT form a virtuous triangle of control, improvement and rapid reactivity to market changes, making the company truly resilient and competitive.
6
Conclusion: Digital Transformation as a Corporate Mindset
RIMSA’s journey illuminates a key truth: Industry 4.0 is not just about upgrading hardware or deploying the latest software. It fundamentally involves organizational culture.
Every function—from R&D and procurement to quality control and assembly—must integrate around a unified digital platform. Employee training and an ethos of collaboration are the catalysts for success.
The rewards are evident: improved oversight, lower costs, less waste, reduced energy consumption, transparency, and robust traceability. On the human side, digital workflows stimulate professional growth, spark creativity, and boost job satisfaction. When data flows freely and machines are networked, it’s easier to assure systematic quality and deliver reliable, meticulously documented products.
Ultimately, digital transformation is an ongoing process rather than a one-and-done achievement. Continuous improvement, workforce upskilling, and strategic tech adoption keep companies future-ready. RIMSA’s approach illustrates how even small to mid-sized enterprises can spearhead digital innovation and assume a leading position in their industry.